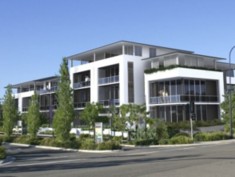
Workplace electronic test equipment - isn't just for electricians (June 2017)
In case you had wondered about workplace electronic test equipment, it isn't just for electricians. This equipment is available for those qualified in the UEENEEE101A Apply Occupational Health and Safety Regulations, codes and practices in the workplace and the UEENEEP026A Conduct in service safety testing of electrical cord assemblies and cord connected equipment courses. Which means you can become qualified to test equipment in your organization.
We will look at a range of products available, what they do and how they could help you if you're needing workplace electronic test equipment. Here is an overview.
Portable Appliance Testers A Portable Appliance Tester (PAT) is an electronic instrument that automatically tests equipment plugged into it. The results it indicates require no technical interpretation. A product like the U-Test 376T has features like:
- Fully battery operated for ease of mobility
- The test result is given not only as an overall pass or fail, but also provides the results of each individual test performed
- Fast test results
If you want a PAT that offers Bluetooth connectivity, you would want to consider the Metrex Delta GT MI 3309 Bluetooth. Some of its features are:
- Test data capture - upload test results to your computer
- Large flash memory, stores approximately 1500 tests
- USB & RS232C for communicating with your computer and barcode reader
- Programmable limits for pass/fail evaluation
- Comes with software
The range is vast, from portable and good value to other high-end PATs available which offer far more including incorporating RCD testing.
Residual Current Devices (RCD) Testers An RCD is an electrical safety device specially designed to immediately switch the electricity off when electricity is detected leaking to the earth at a level harmful to a person using the electrical equipment. It protects against electric shock.
The RCD testers range from digital to others offering a range of features. The SEW RCD Tester 4112 EL, for instance offers key features such as:
- Variable current settings: from 3mA, to 500mA
- Current selection: rotary switch
- Phase start selection : 0 ~ 180 degree
- Phase polarity trip indicator
Three phase adaptors A number are on offer including a cost effective adaptor for testing both 4 & 5 pin 3 phase equipment 10A, 16A, 20A and 32A where a leakage test is not required to a more upmarket adaptor which provides users with more extensive in relation to carrying out a leakage current test. And it displays test results.
Software Software which provides powerful test appliance record and asset management software is available. This means you'll no longer need traditional log books and spread sheet records.
Calibration Your Portable Appliance Tester (PAT) is required to have its calibration checked on a regular basis in accordance with the manufacturer's instructions, with 12 months being the normal recommended minimum time frame.
There are many different pieces of equipment available on the market which can sometimes be confusing if you are not sure what will suit your requirements specifically. If you need a hand selecting the right equipment for your electrical testing please feel free to contact us here. To find out more about our products you can check out the range here.
Electrical Testing - Classes of Equipment (March 2017)
We've previously mentioned during the test tag course that electricity, as we all know, can be dangerous and can kill. Electrical fatality statistics show that the most potentially lethal situations are: incorrectly connected or broken earth conductors, insulation breakdown or working on live. This is why we will outline electrical equipment testing - classes of equipment and why it's important to know these.
There are two classes of equipment. Class I covers areas such as basic insulation and protective earthed equipment. Equipment in which protection against electric shock does not rely on basic insulation only, but has additional safety precautions, in that conductive accessible parts are connected to the protective earthing conductor in the fixed wiring of the installation in such a way that those accessible parts cannot become live in the event of a failure of the basic insulation.
Examples of Class I equipment includes but is not limited to:
- Bench grinders
- Older power tools such as drills, grinders etc.
- Air compressors
- Electric concrete mixers
Class II equipment covers double insulated equipment. This is usually manufactured with non-conductive (insulated) enclosure (normally plastic) and is marked with the words double insulated.
- Class II equipment may also be manufactured with metal enclosures which are double insulated from live parts
- Class II equipment does not need an earth conductor and should not be earthed.
- Most modern power tools and equipment which is subject to movement or flexing of the cord fall in to this category. If you are unable to find the symbol which marks as Class II, treat as a Class 1.
You also need to know about cord set as this includes extension leads and detachable leads supplying power to the equipment, such as those used to connect computers, monitors and printers etc. Commonly called power boards Electric Portable Outlet Device (EPOD) have a single means to connect to a power supply, with one or more outlet facilities.
Then there's Residual Current Devices (RCD). RCDs are commonly known as Earth Leakage Circuit Breakers (ELCB) or safety switches. An RCD is an electrical safety device specially designed to immediately switch the electricity off when electricity is detected leaking to the earth at a level harmful to a person using the electrical equipment.
An RCD offers a high level of protection from electric shock but it will not protect in all instances of electric shock Be aware that double adaptors, domestic type power boards and similar fittings are not permitted for construction work and must not be used.
To find out more about our electrical equipment testing, register for one of our test & tag courses here.
Higher Risk Work Environments and Electrical Tagging (Oct 2016)
There are a number of important points you will need to keep in mind in relation to higher risk work environments and electrical tagging.
As you would imagine, there are numerous requirements that need to be complied with and upheld in certain situations involving high risk work environments and electrical tagging. Firstly, you must comply with the regulations AS NZS 3012-2010 electrical installations - construction and demolition sites.
As well, a person conducting a business or undertaking with management or control of electrical equipment must ensure that the electrical equipment is regularly inspected and tested by a competent person if the electrical equipment in high risk environments and electrical tagging is involved. They are:
Supplied with electricity through an electrical socket outlet (plug in equipment);used in an environment in which its normal use exposes the equipment to operating conditions that are likely to result in damage to the equipment or a reduction in its expected life span.
This includes conditions that involve exposing the electrical equipment to moisture, heat, vibration, mechanical damage, corrosive chemicals.
Inspection and testing or electrical tagging requirements apply in relation to certain higher-risk workplaces, these are often referred to as hostile operating environments, in which electrical equipment is exposed to operating conditions that are likely to result in damage to the equipment or a reduction in its expected life span, and construction and demolition sites.
These kinds of workplaces have operating environments that have the potential to seriously affect the safe operation of electrical equipment. This includes conditions that involve exposing the electrical equipment to moisture, heat, vibration, mechanical damage, corrosive chemicals and dust. Examples of these sorts of conditions include: wet or dusty areas, outdoors, workplaces that use corrosive substances, commercial kitchens, and manufacturing environments.
Inspection and testing, including electrical tagging, of electrical equipment must be carried out more often in these higher risk workplaces and it’s important to always keep that in mind.
Electrical Test and Tag Course for Specific Hazard & Risk Control (Sept 2016)
In the electrical test and tag course you will become familiar with what you will need to know about specific hazard and risk control.
The most common electrical risks of an electrical shock or fire and the subsequent causes of injury are: electric shock causing injury or death. The electric shock may be received by direct or indirect contact, tracking through or across a medium, or by arcing
Electric shock may result from indirect contact where a conductive part which is not normally energised becomes energised due to a fault like a metal toaster body or a fence.
Another hazard is arcing, explosion or fire causing burns. Injuries occur because arcing or an explosion - or both - occur when high fault currents are present.
There is also electric shock from step-and-touch potentials. Or toxic gases causing illness or death as burning and arcing associated with electrical equipment may release various gases and contaminants.
A common hazard is fire resulting from an electrical fault. Contact with electricity can result in serious injury or death. Even the briefest contact with electricity at 50 volts for alternating current (V AC) or 120 volts for direct current (V DC) can have serious consequences to a person’s health and safety. High voltage shocks involving more than 1000 V AC or 1500 V DC can cause contact burns and damage to internal organs.
So who are the individuals who must manage electrical risks? During the electrical test and tag course you will learn that a PCBU (Person Conducting a Business or Undertaking) has the primary duty under the Work Health and Safety (WHS) Act to ensure, so far as is reasonably practicable, that workers and other people are not exposed to electrical risks arising from the business or undertaking. This duty requires eliminating electrical risks, or if that is not reasonably practicable, minimising the dangers.
During the test and tag course, you will discover that there are a number of simple things you need to do to help ensure electrical safety at the workplace. They include:
- Ensure power circuits are protected by the appropriate rated fuse or circuit breaker to prevent overloading;
- If the circuit keeps overloading, don’t increase the fuse rating as this creates a fire risk due to overheating;
- Arrange electrical leads so they will not be damaged;
- Avoid using leads and tools in damp or wet conditions unless they are specially designed for that possibility;
- Ensure residual current devices (RCDs) are effective by regular testing.
How an electrical tagging course can save your business & your life (Aug 2016)
Specified electrical equipment and safety switches in the workplace or in industry need to be tested at fairly regular intervals because as we all know electricity can cause serious physical harm and even kill you, and that’s obviously one of the crucial reasons why an electrical tagging course can save your business and your life.
An electrical tagging course would outline in detail how a Person Conducting a Business or Undertaking (PCBU) or a self-employed person has the responsibility to be confident that the electrical equipment in their workplace is safe and where required, regularly inspected, tested and maintained.
An electrical tagging course would detail how a system should be in place to assess the electrical equipment that is used in the workplace. If the electrical equipment operates in, or is affected by, a hostile environment (this could include mechanical damage, vibration, corrosive substances or dust)
It must be regularly inspected, tested and maintained by a competent person.
An electrical tagging course’s objective is to give the participant the necessary knowledge and practical skills to operate under the umbrella of our country’s Work Health and Safety Act or regulations.
These include: getting to know the Australian Standards AS/NZS 3760:2010 which covers the in-service safety inspection and testing of electrical equipment; as well as the Australian Standards ASNZS3190:2009, which deals with the approval and test specification - residual current devices (current operated earth-leakage devices). Next comes the Australian Standard AS/NZS 3012:2010 which is linked to construction and demolition sites.
The electrical tagging course would also look at the code of practice covered in Managing Electrical Risks in the Workplace 2014 and would also examine manufacturers operating instructions.
The objectives of the electrical tagging course would be for the participant to:
- Understand the application and requirements of the relevant codes of practice (some mentioned above) including AS/NZS 3012:2010;
- Be able to use a Portable Appliance Tester (PAT) safely and effectively;
- Have a clear understanding of the dangers of electricity, its workings and its components;
- Be clear on the need for inspection and testing and when it’s applicable;
- Determine the equipment class (Class I and Class II) in accordance with Australian Standards and the code of practice;
- Understand various important terms: including double insulation, protective earth, insulation resistance and earth leakage current;
- Inspect, test, tag, and complete documentation on the outcome.
NEW TRAINING PACKAGE
Energy Utilities Industry Skills Council Ltd trading as EE-Oz Training Standards is the Australian Government declared Industry Skills Council for the ElectroComms and EnergyUtilities industries.
EE-Oz Training Standards is the body responsible for developing and maintaining the National Qualifications within the National Training Packages under its coverage. These include the Electrotechnology Training Packages.
All Training Packages are reviewed periodically. The previous unit of competency “UEENEEP008B Conduct in-service safety testing of electrical cord connected equipment and cord assemblies” has been be replaced with a new version of the unit competency “UEENEEP026A Conduct in-service safety testing of electrical cord connected equipment and cord assemblies” from the new Training Package UEE11.
What is the difference between the two units? The new unit has a prerequisite unit of competency “UEENEEE101A Apply Occupational Health and Safety Regulations, Codes and Practices in the workplace”.
What does this mean to you? Now that the new unit has been introduced, instead of just attending a one day test and tag course you will be required to complete the unit of competency UEENEEE101A as well. We provide this extra WHS unit online which takes around 2 to 3 hours to complete.
Please be aware that any training company that is not delivering this extra unit for test and tag training is not providing Nationally Recognised Training and as such you may not be fully qualified.
RESIDUAL CURRENT DEVICES IMPORTANT INFORMATION
WorkCover NSW has introduced requirements for Residual current devices (RCDs).
RCD's are commonly referred to as ‘safety switches’. They are an electrical safety device designed to immediately switch off the supply of electricity when electricity leaking to earth is detected at harmful levels. RCDs offer high levels of personal protection from electric shock. Workplace fatalities can be prevented by the use of properly installed and maintained RCDs.
Requirements for residual current devices
Requirements for residual current devices (RCDs) applied to workplaces where ‘plug in’ electrical equipment (electrical equipment supplied with electricity through a socket outlet) is used in the following operating environments:
- electrical equipment is exposed to operating conditions that are likely to result in damage to the equipment (or a reduction in its expected life span) including conditions that involve exposure to moisture, heat, vibration, mechanical damage, corrosive chemicals or dust.
- electrical equipment is moved between different locations in circumstances where damage to the equipment or to a flexible electricity supply cord is reasonably likely
- electrical equipment is frequently moved during its normal use
- electrical equipment forms part of, or is used with, an amusement device.
If electricity is supplied through a socket outlet that does not exceed 20 amps, then the RCD must have a tripping current that does not exceed 30 milliamps. This does not apply if the supply of electricity to the electrical equipment:
- does not exceed 50 volts alternating current
- is direct current
- is provided through an isolating transformer that provides at least an equivalent level of protection
- is provided from a non earthed socket outlet supplied by an isolated winding portable generator that provides at least an equivalent level of protection.
Information about the advantages and disadvantages of different kinds of non portable and portable RCDs are described in Appendix B in the code of practice Managing electrical risks at the workplace. You may need to seek technical advice from a competent person about the kinds of RCDs that are appropriate for your workplace.
Testing of residual current devices
The person with Management or control of a workplace must ensure that RCDs used at a workplace are tested regularly by a competent person to ensure the devices are working effectively. A record of testing (other than daily testing) must be kept until the device is next tested or disposed of. The code of practice Managing electrical risks at the workplace provides more information about electrical work and risk controls.
|